![]() | ![]() | ![]() ![]() ![]() ![]() ![]() ![]() ![]() | ||
![]() | ||||
НОРМАТИВНЫЕ ДОКУМЕНТЫ![]() | ![]() | Более 1000 нормативных документов в разделе ЗАКОНЫ, удобный поиск! | ||
![]() | ![]() |
![]() |
| |||||||||
![]() | ||||||||||
| ППБ | НПБ | СНИПы | ГОСТы | РД | ПУЭ | Правовые акты | Лицензирование | | ||||||||||
![]() |
Поиск идет по названию и сокращенному названию документа в тех разделах, где проставлены "галки". Если ни один из разделов не помечен, то поиск идет по всем разделам. В поиске старайтесь использовать корень ключевого слова. Вывод списка из большого (более 200) числа ссылок занимает некоторое время. Старайтесь сокращать список. |
Издание НЕ официальное [по материалам ВНИИПО] |
ГОСУДАРСТВЕННЫЙ СТАНДАРТ РОССИЙСКОЙ ФЕДЕРАЦИИ
УСТАНОВКИ ВОДЯНОГО И ПЕННОГО ПОЖАРОТУШЕНИЯ АВТОМАТИЧЕСКИЕ.
КЛАПАНЫ УЗЛОВ УПРАВЛЕНИЯ ОБЩИЕ ТЕХНИЧЕСКИЕ ТРЕБОВАНИЯ.
МЕТОДЫ ИСПЫТАНИЙ
ГОСТ Р 51052-97
ГОСУДАРСТВЕННЫЙ СТАНДАРТ РОССИЙСКОЙ ФЕДЕРАЦИИ УСТАНОВКИ ВОДЯНОГО И ПЕННОГО ПОЖАРОТУШЕНИЯ АВТОМАТИЧЕСКИЕ КЛАПАНЫ УЗЛОВ УПРАВЛЕНИЯ ГОСТ Р 51052-97 Общие технические требования. Методы испытаний. Automatic water and foam fire extinguishing installations. Shut-down valves . General technical requirements. Test methods.
Дата введения 1998-01-01
1 ОБЛАСТЬ ПРИМЕНЕНИЯ
Настоящий стандарт распространяется на вновь разрабатываемые и выпускаемые клапаны узлов управления спринклерных и дренчерных установок пожаротушения, предназначенные для пуска огнетушащего вещества и выдачи управляющего импульса для сигнала тревоги о их срабатывании.
Требования настоящего стандарта являются обязательными.
2 НОРМАТИВНЫЕ ССЫЛКИ
2.1 В настоящем стандарте использованы ссылки на следующие стандарты:
ГОСТ 2.601-95 ЕСКД. Эксплуатационные документы
ГОСТ 12.2.003-91 ССБТ. Оборудование производственное. Общие требования безопасности
ГОСТ 12.2.063-81 ССБТ. Арматура промышленная трубопроводная. Общие требования безопасности
ГОСТ 12.4.026-76 Цвета сигнальные и знаки безопасности
ГОСТ 27.301-95 Надежность в технике. Расчет надежности. Основные положения
ГОСТ 27.410-87 Надежность в технике. Методы контроля показателей надежности и планы контрольных испытаний на надежность
ГОСТ 15150-69 Машины, приборы и другие технические изделия. Исполнение для различных климатических районов. Категории, условия эксплуатации, хранения и транспортирования в части воздействия климатических факторов внешней среды
ГОСТ 18321-73 Статистический контроль качества. Методы случайного отбора выборок штучной продукции
ГОСТ 26104-89 Средства измерений электронные. Технические требования в части безопасности. Методы испытаний
ГОСТ Р 50680-94 Установки водяного пожаротушения автоматические. Общие технические требования. Методы испытаний
3 ОПРЕДЕЛЕНИЯ
3.1 В настоящем стандарте применяют следующие термины с соответствующими определениями:
3.1.1 клапан спринклерный: Клапан, предназначенный для спринклерных установок пожаротушения.
3.1.2 клапан дренчерный: Клапан, предназначенный для дренчерных установок пожаротушения.
3.1.3 клапан спринклерно-дренчерный: Клапан, предназначенный для спринклерных и дренчерных установок пожаротушения.
3.1.4 комбинированный привод клапана: Привод клапана, сочетающий два или более типов исполнения привода.
3.1.5 запорное устройство: Подвижный узел клапана, предназначенный для перекрытия его проходного сечения.
4 КЛАССИФИКАЦИЯ, ТИПЫ И ОСНОВНЫЕ ПАРАМЕТРЫ
4.1 По назначению клапаны подразделяют на:
- спринклерные (С);
- дренчерные (Д);
- спринклерно-дренчерные (СД).
4.2 По типу исполнения привода клапаны подразделяют на:
- с гидравлическим приводом (Г);
- с пневматическим приводом (П);
- с электрическим приводом (Э);
- с механическим приводом (М);
- с комбинированным приводом (К).
4.3 По направлению потока жидкости клапаны подразделяют на:
- прямоточные (П);
- угловые (У).
4.4 По рабочему положению на трубопроводе клапаны подразделяют на:
- вертикальные (В);
- горизонтальные (Г);
- универсальные (У).
4.5 Клапаны должны иметь следующую структуру обозначения:
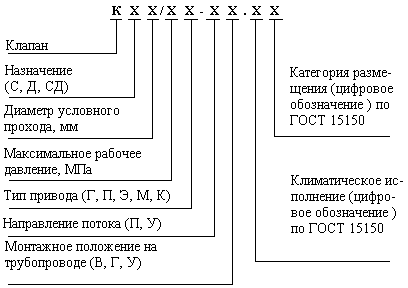
Примечания
1 Для спринклерных клапанов тип привода не проставляют.
2 Монтажное положение на трубопроводе типа У можно не проставлять.
Примеры условных обозначений:
клапана спринклерного с условным диаметром прохода 100 мм, максимальным рабочим давлением 1,2 МПа, прямоточного, с вертикальным монтажным положением, климатическим исполнением О, категорией размещения 4
Клапан КС 100/1,2-ПГ, 04 ГОСТ Р 51052-97
клапана дренчерного с условным диаметром прохода 150 мм, максимальным рабочим давлением 1,6 МПа, приводом электрическим, прямоточного, с любым монтажным положением на трубопроводе, климатическим исполнением О, категорией размещения 4
Клапан КД 150/1,6Э-П, 04 ГОСТ Р 51052-97
4.6 Условный диаметр прохода клапанов должен составлять: 25, 32, 50, 65, 80, 100, 150, 200 и 250 мм.
4.7 Минимальное рабочее давление - не более 0,14 МПа, максимальное давление рабочей среды - не менее 1,2 МПа.
4.8 Напряжение питания электропривода клапанов с электропуском должно быть: 220 В - переменного тока или 24 В - постоянного тока.
5 ТЕХНИЧЕСКИЕ ТРЕБОВАНИЯ
5.1 Клапаны следует изготавливать в соответствии с требованиями настоящего стандарта по рабочим чертежам, утвержденным в установленном порядке.
5.2 Клапаны должны срабатывать в пределах рабочих давлений.
5.3 Время срабатывания клапанов от основного привода не должно превышать 2 с.
5.4 Клапан должен выдерживать пробное гидравлическое давление, равное четырехкратному максимальному рабочему давлению.
5.5 Запорное устройство спринклерного клапана должно обеспечивать герметичность при гидравлическом давлении над выходной полостью (0,015 ± 0,010) МПа.
5.6 Дренчерные клапаны должны обеспечивать герметичность запорного устройства от (0,07 ± 0,01) МПа до 2 Рраб.max.
5.7 Рабочая полость клапана, которая по условиям эксплуатации может находиться под давлением воздуха, должна обеспечивать герметичность при воздействии пневматического давления (0,60 ± 0,03) МПа.
5.8 Коэффициенты потерь напора в клапанах в зависимости от диаметра не должны превышать значений, приведенных в таблице 1.
Таблица 1
Условный диаметр Коэффициент потерь напора воды Расход воды, л/мин 25 2,47 х 10 – 1 300 32 8,65 x 10 – 2 400 50 1,83 x 10 – 2 600 65 5,34 x 10 – 3 800 80 4,23 x 10 – 3 1300 100 3,11 x 10 – 3 2200 150 7,83 x 10 – 4 5000 200 l,98 x 10 – 4 8700 250 1,00 x 10 – 4 14000
5.9 Клапан должен выдерживать расход воды согласно таблице 1.
5.10 Клапан должен сохранять работоспособность после 5000 циклов срабатывания.
5.11 Клапан должен выдерживать гидроудар - циклическое давление, изменяющееся от (0,4 ± 0,1)МПа до (2,50 ± 0,25) МПа.
5.12 Клапан должен выдерживать вибрацию частотой от 5 до 40 Гц и амплитудой 0,1 мм.
5.13 Запорное устройство клапана, заполненного водой и находящегося под давлением (0,35 ± 0,05) МПа, должно быть работоспособно после продолжительной выдержки при температуре (87 ± 2) ° С.
5.14 В клапанах (кроме спринклерных) должно быть предусмотрено местное ручное управление.
5.15 Усилие приведения клапанов (кроме спринклерных) в действие вручную - не более 100 Н.
5.16 Для подсоединения линии сигнализатора срабатывания должно быть предусмотрено технологическое отверстие диаметром не менее 5 мм для dy до 100мм и диаметром не менее 10 мм для dy >100 мм; для слива воды из клапана должно быть предусмотрено технологическое отверстие диаметром не менее 10 мм для dy до 50 мм, диаметром не менее 20 мм - для dy от 50 до 100 мм и диаметром не менее 50 мм - для dy > 100 мм.
5.17 Клапаны должны быть окрашены в красный цвет по ГОСТ 12.4.026 и ГОСТ Р 50680.
5.18 В конструкции клапана должен быть обеспечен удобный доступ для контроля запорного органа; должна быть предусмотрена возможность устранения повреждений деталей и сборочных единиц проточной части, а также возможность замены деталей, подверженных усиленному износу.
5.19 Клапан должен выдавать сигнал срабатывания при расходе воды через него (0,45 ± 0,04) л/с и давлении не более 0,14 МПа.
5.20 Потребляемая мощность электропривода клапана должна быть не более 300 Вт.
5.21 Электрическое сопротивление изоляции токоведущих цепей, с которыми возможно соприкасание человека должно быть не менее 20 МОм.
5.22 По устойчивости к климатическим воздействиям клапаны должны соответствовать требованиям ГОСТ 15150.
5.23 Вероятность безотказной работы клапана в режиме ожидания должна быть не менее 0,99 за время работы не менее 2000 ч.
5.24 Назначенный срок службы - не менее 10 лет.
6 ТРЕБОВАНИЯ БЕЗОПАСНОСТИ
6.1 Требования безопасности - по ГОСТ 12.2.003 и ГОСТ 12.2.063, а также согласно Правилам устройства электроустановок.
6.2 На корпусе электромеханических клапанов с напряжением питания 220 В должна быть предусмотрена клемма заземления. Заземление корпуса электромеханических клапанов должно выполняться по ГОСТ 26104.
7 КОМПЛЕКТНОСТЬ
К каждому клапану должна быть приложена эксплуатационная документация по ГОСТ 2.601:
- техническое описание, инструкция по монтажу и эксплуатации клапанов;
- паспорт на клапан (или паспорт, совмещенный с техническим описанием и инструкцией по эксплуатации);
- паспорта на комплектующее оборудование и приборы, а также инструкции по их эксплуатации;
- чертежи деталей, подверженных усиленному износу;
- монтажные чертежи, электрические и гидравлические схемы;
- ремонтная документация;
- ЗИП.
8 ПРАВИЛА ПРИЕМКИ
8.1 Клапаны следует подвергать испытаниям: приемо-сдаточным, периодическим, типовым, контрольным на надежность и сертификационным.
8.2 Каждый клапан следует подвергать приемо-сдаточным испытаниям. Номенклатура параметров, которые проверяют в процессе этих испытаний, приведена в таблице 2.
8.3 Периодические испытания проводят не реже одного раза в год из числа клапанов, прошедших приемо-сдаточные испытания. Номенклатура параметров, которые проверяют в процессе периодических испытаний, приведена в таблице 2, количество испытываемых образцов не менее трех.
8.4 Типовые испытания проводят при изменении технологии изготовления, замене материала и других изменениях в полном объеме испытаний, количество испытываемых образцов не менее 3.
8.5 Испытания на надежность проводят не реже одного раза в три года.
8.6 Сертификационные испытания проводят в полном объеме периодических испытаний (таблица 2), за исключением 5.1 (в части проверки соответствия чертежам), 5.13, 5.23, 5.24.
8.7 Все испытания проводят при нормальных климатических условиях по ГОСТ 15150.
Таблица 2
Номенклатура испытаний и проверок Пункты настоящего стандарта Необходимость проведения испытаний Технических требований методов испытаний при приемосдаточных испытаниях при периодических испытаниях 1 Визуальный осмотр 5.1 9.1 + + 2 Проверка на соответствие чертежам 4.6, 5.1 9.2 + - 3 Проверка срабатывания 4.7, 5.2 9.3 + - 4 Проверка напряжения питания 4.8 9.4 - + 5 Испытание на время срабатывания 5.3 9.5 - + 6 Испытание на прочность гидравлическим давлением 5.4 9.6 + - 7 Испытание на герметичность запорного устройства спринклерного клапана 5.5 9.7 + - 8 Испытание на герметичность запорного устройства дренчерного клапана 5.6 9.8 + - 9 Испытание на герметичность рабочей полости спринклерного клапана пневматическим давлением 5.7 9.9 + - 10 Проверка коэффициента потерь напора воды 5.8 9.10 + - 11 Испытание на прочность расходом воды 5.9 9.11 - + 12 Проверка работоспособности (число циклов срабатывания) 5.10 9.12 - + 13 Испытание на устойчивость к гидроудару 5.11 9.13 - + 14 Испытание на виброустойчивость 5.12 9.14 - + 15 Испытание запорного устройства клапана на работоспособность 5.13 9.15 - + 16 Проверка местного ручного управления 5.14 9.16 + - 17 Испытание на усилие приведения в действие 5.15 9.17 - + 18 Проверка диаметра технологических отверстий 5.16 9.18 + - 19 Проверка цвета окраски клапана 5.17 9.19 - + 20 Проверка удобства доступа для контроля запорного органа 5.18 9.20 - + 21 Проверка выдачи сигнала о срабатывании сприн-клерного клапана 5.19 9.21 - + 22 Проверка потребляемой мощности 5.20 9.22 - + 23 Испытание на электрическое сопротивление изоляции токоведущих цепей 5.21 9.23 - + 24 Испытание на устойчивость к климатическим воздействиям 5.22 9.24 - + 25 Испытание на вероятность безотказной работы 5.23 9.27 - + 26 Проверка назначенного срока службы 5.24 9.25 - + 27 Проверка маркировки 10.1 9.26 + + Примечание - “+” испытание проводят; “-” испытание не проводят.
8.8 Отбор образцов для испытаний - по ГОСТ 18321. Результаты испытаний и проверок распространяют на всю партию. Партией считают количество клапанов, предъявленных к приемке по одному документу и изготовленных за период не более 30 календарных дней.
8.9 Результаты испытаний считают удовлетворительными, если предъявленные к испытаниям клапаны соответствуют требованиям настоящего стандарта.
8.10 При получении неудовлетворительных результатов по любому из показателей следует проводить повторную проверку на удвоенном количестве объектов испытаний. Если хотя бы один из клапанов дополнительной партии не удовлетворяет типовым требованиям, то клапаны считают не выдержавшими испытания.
9 МЕТОДЫ ИСПЫТАНИЙ
9.1 Все клапаны, подлежащие испытаниям, предварительно осматривают на отсутствие очевидных дефектов.
9.2 Соответствие клапанов требованиям (4.6, 5.1) следует проверять сличением рабочим чертежей с образцом в соответствии с требованиями стандартов и с применением соответствующего измерительного инструмента, обеспечивающего заданную точность измерения.
9.3 Срабатывание клапанов (4.7, 5.2) определяют при минимальном и максимальном давлениях перед запорным устройством. Критерием положительной оценки срабатывания является полное открытие запорного устройства.
9.4 Проверку напряжения питания (4.8) осуществляют путем изменения его в пределах
% номинального. На крайних значениях напряжения питания клапан проверяется на срабатывание по 5.2. Количество срабатываний при каждом значении параметра - не менее 3.
Критерием положительной оценки является срабатывание клапанов.
9.5 Время срабатывания клапанов (5.3) определяют при минимальном и максимальном рабочих давлениях перед запорным устройством. Длина отводящего трубопровода (1,0 ± 0,1) м, диаметр выпускного отверстия этого трубопровода (10,0 ± 0,1) мм. При испытании клапана отводящий трубопровод заполняют водой. Срабатывание может осуществляться от любого вида привода или вручную. За время срабатывания принимают интервал времени с момента подачи управляющего импульса до достижения установившегося давления в рабочей полости клапана. Число испытаний при каждом давлении - не менее 3.
За факт срабатывания принимают резкое изменение давления в одной из рабочих полостей.
9.6 Прочность корпуса клапана (5.4) проверяют при открытом запорном устройстве гидравлическим давлением, в 4 раза превышающем его максимальное рабочее давление, в течение не менее 5 мин. Скорость нарастания давления не более 0,1 МПа/с.
Течь, остаточные деформации и разрушение корпуса клапана не допускаются.
9.7 Герметичность запорного устройства спринклерного клапана (5.5) проверяют путем создания в выходной полости клапана гидравлического давления не менее (0,015 ± 0,010) МПа в течение не менее 16 ч. Скорость нарастания давления не более 0,005 МПа/с.
Протечки воды через уплотнение запорного органа не допускаются.
9.8 Испытание на герметичность запорного устройства дренчерного клапана (5.6) проводят при закрытом клапане при гидравлическом давлении во входной полости (0,07 ± 0,01) МПа и не менее 2 Рраб.max в течение не менее 5 мин на каждом уровне давления. Скорость нарастания давления не более 0,01 МПа/с. Клапан на каждом уровне давления испытывают не менее 2 раз.
Течь через запорное устройство не допускается.
9.9 Герметичность рабочей полости спринклерного клапана пневматическим давлением (5.7) проверяют при создании в выходной полости клапана пневматического давления (0,60 ± 0,03) МПа в течение не менее 5 мин.
Утечка воздуха не допускается.
9.10 Коэффициент потерь напора в клапане (5.8) определяют при расходе воды, указанном в таблице 1 (допуск на расход ± 5 %). Диаметр трубопровода должен соответствовать условному диаметру прохода клапана.
9.11 Испытание на прочность клапана расходом воды (5.9) проводят при обеспечении расхода через клапан согласно таблице 1. Продолжительность испытаний не менее 30 мин.
Признаки искривления элементов клапана, трещин на корпусе, остаточных деформаций и поломок отдельных частей не допускаются.
9.12 Работоспособность клапана (число циклов срабатывания) (5.10) проверяют при максимальном рабочем давлении. Общее число срабатываний - 5000 циклов, число циклов в минуту - не более 20; срабатывание (полное открытие и закрытие) может осуществляться от любого вида привода или вручную.
За критерий отказа принимают отсутствие срабатывания клапана по 5.2.
9.13 Устойчивость к гидроудару (5.11) проверяют при закрытом клапане путем повышения давления во входной полости от (0,4 ± 0,1) МПа до (2,50 ± 0,25) МПа со скоростью не менее 10 МПа/с. Испытание на каждом клапане проводят 2 раза.
Признаки механического повреждения, остаточных деформаций корпуса и элементов клапана, а также протечки воды через уплотнение не допускаются.
9.14 Испытание клапанов на виброустойчивость (5.12) проводят на вибростенде, при этом клапан крепят к платформе стенда в рабочем положении. Необходимо непрерывно отслеживать частоту вибраций от (5 ± 1) до (40 ± 1) Гц при темпе не более 5 мин/октава и амплитуде 1 мм. При обнаружении резонансных точек необходимо клапан подвергать воздействию вибрации на каждой резонансной частоте в течение 120 ч. Если резонансная частота не установлена, то клапан необходимо подвергать вибрациям на частоте от 5 до 40 Гц с амплитудой 1 мм в течение 120 ч.
После испытаний проводят внешний осмотр клапанов - механические повреждения не допускаются.
9.15 Работоспособность запорного устройства клапана (5.13) проверяют при температуре (87 ± 2) ° С и давлении (0,35 ± 0,05) МПа. Скорость нарастания давления не более 0,1 МПа/с. Клапан должен быть закрыт и установлен таким образом, чтобы вода постоянно контактировала по всей площади с запорным органом и местом уплотнения.
Продолжительность испытаний не менее 90 сут. Признаки прилипания запорного органа к контактирующей с ним поверхности не допускаются.
9.16 Проверку срабатывания клапана при местном ручном управлении (5.14) осуществляют путем соответствующего воздействия на органы управления, смонтированные по типовой для данного вида клапана схеме.
Испытания проводят при минимальном и максимальном давлениях. Число испытаний при каждом давлении не менее трех.
9.17 Проверку усилия приведения в действие клапана вручную (5.15) осуществляют при минимальном и максимальном рабочих давлениях на входе испытываемого устройства на всех предназначенных для этих целей органах управления.
9.18 Проверку диаметра технологических отверстий (5.16) осуществляют измерительным инструментом с погрешностью измерения не более 0,1 мм.
9.19 Проверку цвета окраски клапана (5.17) осуществляют визуально.
9.20 Проверку обеспечения удобного доступа для контроля запорного органа клапана, возможности устранения повреждений деталей и сборочных единиц проточной части, а также возможности замены деталей (5.18), подверженных усиленному износу, осуществляют путем проведения соответствующих операций, связанных с достижением планируемых целей. За критерий удобства принимают использование стандартных инструмента и принадлежностей. Длительность проведения каждой операции должна быть не более 5 мин или продолжительность совокупности всех операций - не более 0,5 ч.
9.21 Выдачу сигнала о срабатывании спринклерного клапана (5.19) проверяют по срабатыванию пожарного сигнализатора, смонтированного в обвязку клапана, при расходе воды через клапан (0,45 ± 0,04) л/с и давлении не более 0,14 МПа.
9.22 Потребляемую мощность (5.20) определяют при напряжении питания соответственно переменным током 220+22 В или постоянным током 24+2,4 В.
9.23 Электрическое сопротивление изоляции токоведущих цепей (5.21) определяют мегомметром. Сопротивление измеряют между каждой клеммой электрического проводника и наружной оболочкой проводника, а также между каждой клеммой электрического проводника и корпусом клапана.
9.24 Испытания на устойчивость к климатическим воздействиям (5.22) проводят на холодоустойчивость и теплоустойчивость при температуре в соответствии с исполнением и категорией по ГОСТ 15150 (теплоустойчивость - не ниже 50 ° С). Клапан выдерживают при соответствующих температурах в течение 3 ч, после чего в нормальных климатических условиях - в течение 3 ч, а затем клапан проверяют на срабатывание по 4.7, 5.2. Признаки механического повреждения корпуса и запорного органа, неполное открытие и закрытие запорного органа не допускаются.
9.25 Контроль назначенного срока службы (5.24) проверяют путем обработки статистических данных [1].
9.26 Проверку маркировки (10.1) осуществляют визуально.
9.27 Испытание на вероятность безотказной работы (на надежность) (5.23) проводят в соответствии с ГОСТ 27.301 и ГОСТ 27.410 одноступенчатым методом. Приемочный уровень вероятности срабатывания клапанов принимается равным 0,99, браковочный уровень вероятности срабатывания - 0,9. Риск изготовителя принимают 0,1, риск потребителя - 0,2. Объем выборки 11 клапанов, приемочное число отказов 0. Продолжительность испытаний не менее 300 ч при давлении (0,14 ± 0,02) МПа и не менее 300 ч при давлении не менее максимального рабочего.
Количество циклов срабатывания (полное открытие и закрытие клапана) должно быть не менее 2 циклов за 1 ч.
В качестве критерия отказа принимают наличие механических дефектов и несоответствие параметрам по 5.5-5.7, 5.19.
10 МАРКИРОВКА
10.1 На каждом клапане должна быть маркировка, содержащая:
- товарный знак предприятия-изготовителя;
- условное обозначение клапана;
- условный диаметр прохода;
- диапазон рабочих давлений;
- стрелку, указывающую направление потока;
- знак рабочего положения клапана в пространстве (если оно ограничено);
- условное обозначение каждого отверстия в корпусе клапана, обеспечивающего его обвязку в узел управления;
- знак заземления (если к клапану подводится напряжение 220 В);
- год выпуска.
10.2 Маркировку следует проходить любым способом, обеспечивающим ее четкость и сохранность в течение всего срока службы клапана.
11 ГАРАНТИИ ИЗГОТОВИТЕЛЯ
11.1 Изготовитель гарантирует соответствие клапана требованиям настоящего стандарта при соблюдении условий транспортирования, хранения, монтажа и эксплуатации, установленных эксплуатационной документацией по ГОСТ 2.601.
11.2 Срок службы - 10 лет.
ПРИЛОЖЕНИЕ А
(информационное)
БИБЛИОГРАФИЯ
[1] РД 50-690-89 Надежность в технике. Методы оценки показателей надежности по экспериментальным данным. Методические указания
1 РАЗРАБОТАН И ВНЕСЕН Техническим комитетом по стандартизации МТК 274/643 “Пожарная безопасность”
2 ПРИНЯТ И ВВЕДЕН В ДЕЙСТВИЕ Постановлением Госстандарта России от 29 апреля 1997 г. № 157
3 ВВЕДЕН ВПЕРВЫЕ
![]() |
![]() ![]() |